Qu'est-ce que la maintenance corrective ?
La maintenance corrective est la catégorie de tâches de maintenance qui sont effectuées pour rectifier et réparer les systèmes et les équipements défectueux. L'objectif de la maintenance corrective est de rétablir les systèmes qui sont tombés en panne. La maintenance corrective peut être synonyme de panne ou de maintenance réactive.
Quand est-ce que la maintenance corrective est-elle nécessaire ?
Les tâches de maintenance corrective peuvent être planifiées ou non planifiées et se produisent pour trois raisons différentes :
1. Lorsque la maintenance conditionnelle met en évidence un problème
2. Lorsqu'un défaut potentiel est détecté lors d'une inspection de routine
3. Lorsqu'une pièce d'équipement tombe en panne
La maintenance corrective est souvent inévitable pour les équipes de maintenance devant répondre aux pannes ou aux défaillances des équipements. Cependant, il peut être néfaste de se fier uniquement à la maintenance corrective plutôt qu'à d'autres types de maintenance, comme la maintenance préventive.
La maintenance corrective convient parfaitement lorsqu'un bien peut être facilement réparé ou remplacé et que les pièces sont disponibles en abondance, mais dans certains cas, elle peut entraîner des temps d'arrêt imprévus et coûteux. Les experts s'accordent à dire que 80 % de votre maintenance doit être préventive et seulement 20 % corrective.
Quels sont les différents types de maintenance corrective ?
Les types de tâches de maintenance corrective peuvent être classés en différentes catégories. Par exemple, l'armée américaine utilise cinq catégories de maintenance corrective dans son manuel de conception technique :
- Réparation des défaillances - Remettre un bien défaillant dans un état opérationnel.
- Révision - Rétablissement complet d'un bien dans son état de service, conformément aux normes de maintenance.
- Récupération - Mise au rebut des pièces qui ne peuvent pas être réparées et remplacement par des pièces de récupération provenant de biens non réparables.
- Entretien - Réparations finales après des actions correctives plus importantes.
- Reconstruction - Démontage des pièces et remplacement des composants usés conformément aux normes et spécifications d'origine.
Chacune de ces cinq catégories de tâches de maintenance corrective peut être programmée ou non.
La maintenance non programmée (ou non planifiée) concerne les réparations effectuées immédiatement, tandis que la maintenance corrective programmée (ou planifiée) concerne les tâches qui peuvent être reportées à une date ultérieure. Ce report peut tenir compte des budgets, des contraintes de temps ou de la dotation en personnel.
Maintenance planifiée / programmée
La maintenance planifiée peut être divisée en deux groupes : la maintenance de type "courir jusqu'à la panne" ou "run-to-failure" et la maintenance préventive. La maintenance de type "Run-to-failure" consiste à laisser fonctionner un bien jusqu'à ce qu'il tombe en panne, après quoi il est réparé ou remplacé. Ce type de stratégie de maintenance corrective ne convient qu'aux systèmes non critiques ou redondants, faciles à remplacer ou à réparer.
La maintenance préventive planifiée, qui est souvent effectuée dans le cadre de la maintenance conditionnelle, consiste à identifier et à traiter les problèmes lors des inspections de maintenance.
Maintenance non programmée / non planifiée
La maintenance corrective est non planifiée soit lorsqu'une panne survient de manière inattendue. Cela peut être dû au fait qu'aucun plan de maintenance n'était en place, ou qu'un actif tombe en panne avant l'inspection ou l'action de maintenance prévue.
Les avantages de la maintenance corrective
La maintenance corrective peut offrir une série d'avantages lorsqu'elle est utilisée dans le cadre d'un programme de maintenance plus large. Ces avantages sont les suivants
- Réduction de la planification : La maintenance corrective nécessite moins de planification que la maintenance préventive, même lors de la programmation des réparations.
- Processus simple : La maintenance corrective est un processus simple qui est basé sur les besoins, permettant aux équipes de maintenance de se concentrer sur d'autres domaines jusqu'à ce que cela soit nécessaire.
- Coûts moindres à court terme : Ce type de maintenance peut être plus rentable à court terme, car le travail n'est effectué que lorsque cela est nécessaire. Ceci est vrai pour les réparations ou les remplacements simples, comme une ampoule grillée qui peut être réparée rapidement sans le temps et les dépenses d'un plan de maintenance préventive.
- Amélioration de la planification des ressources : Si les ordres de travail de maintenance corrective sont classées par ordre de priorité et programmés, ils peuvent permettre d'optimiser les ressources humaines et financières. Cela peut entraîner une diminution des interruptions de service, car les équipes de maintenance peuvent résoudre les problèmes avant que la production ne soit affectée ou que les services ne soient interrompus.
- Réduction des temps d'arrêt : Si un technicien de maintenance remarque un composant usé lors d'un entretien de routine, une action corrective peut réduire le risque de temps d'arrêt ultérieur dû à une panne.
- Prolongation de la durée de vie des actifs : La maintenance corrective peut prolonger la durée de vie des actifs critiques si les pièces sont réparées ou remplacées avant qu'elles n'affectent d'autres parties de la machine.
Les inconvénients de la maintenance corrective
Malgré les avantages de la maintenance corrective, cette méthode présente également certains inconvénients, en particulier lorsqu'elle ne s'appuie pas sur une stratégie de maintenance préventive. Ces inconvénients sont les suivants
- Des coûts de maintenance à long terme plus élevés : Le simple fait de faire fonctionner les actifs jusqu'à ce qu'ils se cassent peut entraîner des coûts de maintenance à long terme plus élevés, car l'état de l'équipement se détériore avant que les problèmes ne soient découverts. D'autres composants peuvent alors être affectés et davantage de pièces doivent être réparées ou remplacées, avec les coûts de main-d'œuvre associés.
- Questions de sécurité : La pression exercée pour réduire les coûts de maintenance inattendus peut également créer des problèmes de sécurité, car les travaux de réparation peuvent être précipités et peut ne pas être effectués correctement. De plus, faire tourner une machine jusqu'à ce qu'elle se casse peut entraîner des risques potentiels pour le personnel qui l'utilise.
- Imprévisibilité : L'inconvénient le plus important est la nature imprévisible de la maintenance corrective. Si un bien tombe en panne de manière inattendue, cela peut perturber d'autres travaux de maintenance et entraîner des temps d'arrêt imprévus. La maintenance peut être lente et coûteuse, car il faut trouver la cause de la panne et commander des pièces de rechange pour effectuer une réparation. En raison de la nature réactive de la maintenance corrective, les équipements ne sont pas optimisés et la production peut chuter. L'imprévisibilité n'est pas un problème dans le cas de petites réparations (comme le remplacement d'une ampoule grillée), mais elle peut l'être dans le cas de pannes plus importantes. Ce problème peut être évité grâce à une stratégie de maintenance plus proactive et prédictive.
Exemples de maintenance corrective
Il existe plusieurs différences subtiles dans les types de maintenance corrective qui peuvent être effectués. Des exemples de maintenance corrective peuvent démontrer ces différences, par exemple :
Maintenance corrective de type Run-to-Fail
Un exemple de ce type de maintenance corrective concerne les ampoules et autres composants non essentiels et faciles à remplacer. Dans ce cas, un stock de pièces de rechange peut être conservé sur place et installé lorsque la dernière tombe en panne.
Maintenance corrective planifiée
Ce type de maintenance va souvent de pair avec les routines de maintenance préventive. Par exemple, vous pouvez avoir une bande transporteuse de ligne de production dont l'usure est régulièrement inspectée. Une inspection révèle que certains roulements doivent être remplacés et un ordre de maintenance corrective est alors programmé. Par ailleurs, un technicien peut répondre à un problème, tel qu'un moteur qui a des ratés, et découvrir un autre problème, comme un filtre bouché. Une demande de maintenance corrective planifiée peut alors être déposée pour nettoyer ou remplacer le filtre. Ce type de maintenance concerne toujours les pannes et les défaillances inattendues, mais les travaux de réparation et de remplacement peuvent être planifiés ou mis en évidence comme potentiellement nécessaires pour une inspection.
Maintenance corrective non planifiée
La maintenance corrective non planifiée se produit généralement lorsqu'aucun plan de maintenance préventive n'a été mis en place. Par exemple, vous pouvez avoir un chariot élévateur à fourche qui n'est pas inspecté, mais qui tombe en panne. La réparation d'un tel élément relève de la maintenance corrective non planifiée. D'autres exemples sont les conduites d'eau qui éclatent et doivent être remplacées rapidement. Cependant, la maintenance non planifiée peut se produire même lorsqu'un plan de maintenance est en place. Par exemple, si vous avez une machine qui doit être inspectée toutes les 100 heures d'utilisation, mais qui tombe en panne après seulement 80 heures, vous devrez effectuer une réparation d'urgence non planifiée. La maintenance non planifiée nécessite souvent une réparation immédiate, mais ne fait pas partie d'un plan visant à laisser le composant tomber en panne, comme c'est le cas pour la maintenance "run-to-fail".
Pourquoi la maintenance corrective est-elle importante ?
La maintenance corrective est importante car elle permet à une installation de retrouver sa pleine efficacité après une panne d'équipement. Les tâches de maintenance impliquent le remplacement ou la réparation d'éléments après leur défaillance et peuvent être classées par ordre de priorité en fonction de leur criticité. Cette priorité comprend des facteurs liés à la sécurité ainsi qu'à la production et aux temps d'arrêt.
Les tâches de maintenance corrective non programmées peuvent ralentir les lignes de production, mais généralement, le temps d'arrêt associé à ces tâches correctives est faible par rapport à une panne totale de l'équipement. L'exécution de ces actions correctives en temps voulu devrait permettre de remettre votre actif en parfait état de marche le plus rapidement possible.
La maintenance corrective peut également intervenir avant la défaillance totale d'un élément. En remarquant l'usure et en remplaçant les composants avant qu'ils ne se cassent, vous pouvez éviter des coûts inutiles et des temps d'arrêt. Ces tâches peuvent être programmées en fonction de leur criticité, ce qui permet de minimiser les pannes d'équipement.
Pourquoi l'entretien correctif est-il coûteux ?
L'entretien correctif est souvent inévitable et comporte, de par sa nature même, des coûts imprévus. Cependant, à court terme, l'entretien correctif peut en fait permettre d'économiser de l'argent.
Ce type de maintenance n'utilise pas beaucoup de ressources en termes d'outils, de temps, de technologie ou d'expertise. Laisser délibérément quelque chose fonctionner jusqu'à la panne ou ne pas mettre en œuvre un plan de maintenance prédictive est une bonne chose pour les pièces moins critiques, peu coûteuses, facilement disponibles et faciles à remplacer. Toutefois, cette pratique est inefficace en tant que méthode de travail générale et peut entraîner des dépenses plus importantes si une défaillance entraîne la défaillance d'autres pièces et une éventuelle défaillance catastrophique de l'ensemble du bien. Des problèmes aussi graves peuvent entraîner de longues périodes d'immobilisation, des réparations coûteuses, voire la nécessité de remplacer une pièce d'équipement entière. Tous ces facteurs peuvent rapidement entraîner une augmentation considérable des coûts.
En outre, la maintenance corrective n'a pas tendance à prendre en compte les causes d'un problème, ce qui peut entraîner des défaillances répétées des pièces de rechange ultérieures et les coûts de réparation et de remplacement associés.
Conclusion
La maintenance corrective est une chose à laquelle toutes les installations doivent faire face, mais elle ne doit pas nécessairement être un processus coûteux. S'il n'y a pas de problème à laisser certaines pièces non critiques, peu coûteuses et faciles à remplacer, il faut tout de même un certain niveau de préparation pour s'assurer que les pièces de rechange sont disponibles en stock et qu'il y a quelqu'un qui peut les installer.
Pour tirer le meilleur parti de la maintenance corrective, il est préférable de la coupler à des tâches de maintenance préventive afin que les employés puissent signaler tout problème. Cela permettra de planifier la maintenance à un moment opportun, avant qu'une défaillance critique ne survienne.
Une maintenance corrective critique et non planifiée peut s'avérer coûteuse, tant en termes de coûts de main-d'œuvre que de temps d'arrêt. Il vaut donc la peine, à long terme, d'optimiser la maintenance corrective planifiée pour que vos actifs fonctionnent au maximum de leur efficacité.
Qu'est-ce que propose Spectral TMS ?
Spectral TMS offre un service de réalité augmentée de soutien à la production à ses membres industriels, y compris la gestion des actifs et l'analyse et la réparation des défaillances. Nos experts ont pour mission d'aider l'industrie à améliorer la qualité, l'efficacité et la rentabilité dans tous les aspects de la technologie d'assemblage des matériaux. Notre solution s'étend actuellement à des entreprises mondialement connues comme Safran, Legrand ou encore Sanofi, mais peut couvrir tous les secteurs industriels.
Vous pouvez en savoir plus en nous contactant ou en prenant rendez-vous, ci-dessous :
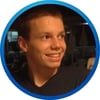
Le :
Par : Arnaud Pringuey, Expert RA en industrie chez Spectral TMS